The Need for Water in Pharma Production, and Considerations of Water Scarcity
The issue of water scarcity is on the rise, and this problem is becoming more prominent in various industries. Water plays a crucial role in nearly every aspect of production, including the pharmaceutical manufacturing sector, which relies heavily on significant water quantities.
Concerns regarding water utilization are escalating in importance, and this trend is poised to persist. In regions grappling with water scarcity, such as the Western United States and Taiwan, reducing water consumption is increasingly mandated for organizations due to the unavailability of sufficient water resources.
Energy Expenses in Water Systems
The associated expenses of both obtaining and disposing of pure water are substantial. Consequently, the importance of implementing methods to reduce water consumption is growing. Specifically, within the pharmaceutical industry, Total Organic Carbon (TOC) analyzers are indispensable tools, yet they can consume large volumes of pure water. The development of water-efficient TOC analyzers is a significant step in minimizing water usage, resulting in cost savings and promoting eco-friendly manufacturing practices.
Escalating Water Costs
The expenses associated with discharging or treating wastewater can soar to levels significantly higher, sometimes even tenfold, than the initial cost of procuring water. Certain regions, such as Germany, impose considerably higher charges for wastewater disposal, resulting in substantial financial burdens for organizations. These cost disparities serve as a strong incentive for companies to prioritize water conservation measures and cost-saving strategies.
Consequently, many businesses have implemented water reuse and recycling initiatives for assets like water cooling towers, introduced gray-water systems for landscaping irrigation, and incorporated drought-resistant plants into their surroundings. In the pharmaceutical sector, the reutilization of wastewater within Reverse Osmosis (RO) systems or other purification methods has gained popularity, significantly reducing wastewater discharge. Several cosmetics companies have also been early adopters of water loop systems in select countries, yielding substantial cost savings running into the tens of millions of dollars.
Hot WFI Exacerbates Energy Use
The environmental impact of water usage within a hot WFI (Water for Injection) system is exacerbated by the energy required to heat the water. This heating process is a significant contributor to carbon dioxide emissions. Consequently, transitioning to an ambient WFI system can have a profound impact on energy costs and diminish the emission of greenhouse gases.
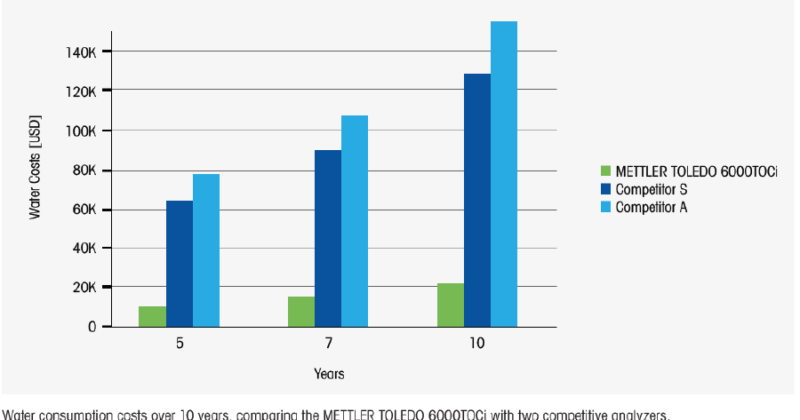
A rough estimate suggests that heating water from 20 to 80°C over the course of a year in a typical process analytical technology (PAT) system used in pharmaceutical water systems could amount to as much as $100 per TOC unit annually, assuming the TOC analyzer operates at a flow rate of 60 mL/min. In contrast, running the 6000TOCi at 8.5 mL/min incurs a significantly lower cost of just $13 per TOC unit per year.
Biologic Drugs’ High Need for Water Resources
The surge in demand for biologic drugs has further exacerbated the need for water resources. Presently, eight of the top ten bestselling drugs on the market are biologics, with familiar names like Humira®. This trend is leading to an exponential growth in the production of biologic drugs, which require cellular systems and, consequently, substantial amounts of water. To meet this surging demand, increasingly larger bioprocess facilities are being established, resulting in elevated costs associated with producing high-purity water and analyzing it.
Corporate Commitments to Sustainability
Many companies have taken proactive steps to embrace sustainability as part of their corporate initiatives. These endeavors encompass the reduction of carbon dioxide emissions, minimizing waste generation, and curbing water consumption. Unlike some common environmental improvements like installing smart thermostats or energy-efficient lighting in office spaces, laboratories and process analytical technologies (PAT) used in manufacturing present unique sustainability challenges.
A prominent illustration of corporate dedication to sustainability can be found in one of the world’s largest biotechnology companies. In 2015, they launched a comprehensive program aimed at combating waste, promoting recycling, reducing water usage, and lowering carbon dioxide emissions through decreased transportation activities. Notably, their efforts underscored that manufacturing processes’ water consumption represented the most substantial portion of their overall water usage.
Striving Towards Water Efficiency in Total Organic Carbon Analysis
Hence, the imperative to reduce water consumption in the biopharmaceutical sector, particularly for essential tasks such as TOC analysis, is growing rapidly. In addition to these efforts, some manufacturing plants are taking proactive steps by installing their own wastewater treatment facilities. This not only ensures a consistent water supply for manufacturers but also aids in complying with evolving, integrated pollution prevention laws, particularly those being enacted in Europe. These measures not only contribute to sustainable water usage but also align with environmental regulations, fostering responsible industrial practices.
Environmental Consequences
Green TOC (Total Organic Carbon) systems contribute positively to our planet. While there is substantial discourse on the cost savings associated with water and energy, it’s crucial to acknowledge that Earth’s freshwater resources are limited, necessitating conservation efforts to preserve the delicate equilibrium of ecosystems we depend on. According to estimates from the World Health Organization (WHO), by 2025, approximately half of the global population will reside in regions facing water scarcity.
Water Efficiency in TOC Measurement
Minimizing water wastage during pharmaceutical and biotech manufacturing processes holds paramount importance. Analyzing water quality is a requisite step in the production of biologic drugs and vaccines today. Nonetheless, the quantity of water utilized for testing crucial parameters like TOC often goes unnoticed.
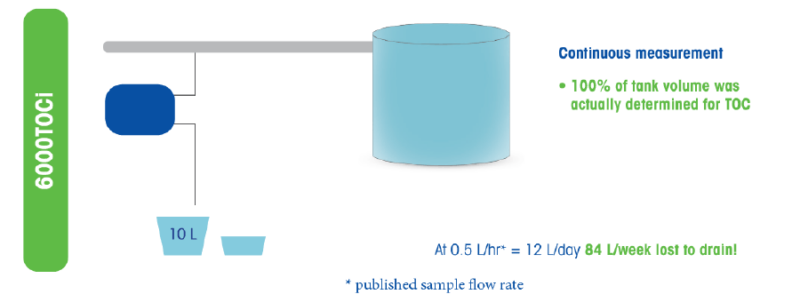
Many preceding-generation TOC monitoring systems employ membrane-based batch techniques, which neither offer truly continuous data nor are water-efficient. Operating at a flow rate of 50-60 mL/min, these systems can result in the disposal of over 600 liters of water every week. Moreover, as batch methods, they carry the risk of overlooking TOC excursions. In contrast, the 6000TOCi sensor provides real-time, continuous TOC monitoring, enhancing process control, and operates at a flow rate of only 8.5 mL/min. This water-efficient sensor discharges only 84 liters of water per week.
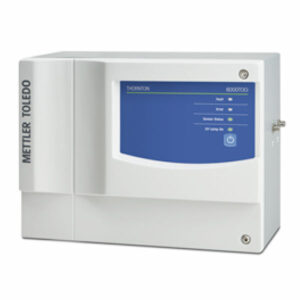
This reduced water consumption significantly reduces waste over the sensor’s lifespan, translating into substantial cost savings for manufacturers. In batch-controlled systems, the potential exists to waste an entire batch of water (equating to several cubic meters) if a TOC excursion goes unaddressed. Furthermore, when installed in hot WFI systems, additional savings accrue when considering the extra costs associated with heating the discarded water.